انتخاب روانکار مناسب تاسیسات دارویی
نویسنده: مهندس علیرضا آمار محمدی -کارشناس ارشد روانکارهای خودرویی و صنعتی
هرگونه مواد مورد نیاز برای عملیات، مانند روانکنندهها یا خنککنندهها، نباید با اجزا، ظروف فرآوردههای دارویی، دربها، مواد در حال فرآیند یا محصولات دارویی در تماس باشند.
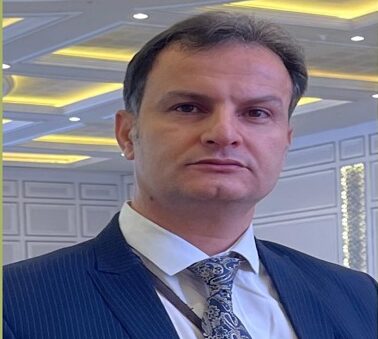
فرهنگ اقتصاد _ با پیشرفت صنعت داروسازی و بهره مندی این صنعت از تجهیزات نوین با تکنولوژی جدید و به تناسب آن استفاده از روانکار مناسب و دارای استانداردهای لازم امری ضروری و اجتناب ناپذیر است.
مهندسان مکانیک و الکترونیک نهایت تلاش خود را می کنند تا ماشینهایی را طراحی نمایند که حداقل نیاز روانکاری را داشته باشد و با اینحال در بعضی از قسمتها مانند نوار نقاله، زنجیرها، کمپرسورها و پمپ ها همچنان نیاز روانکار ضروری دیده می شود.
انتخاب روانکار مناسب با در نظر گرفتن شرایط کاری اعم از فشار و سرعت عملکرد و ویسکوزیته مناسب سیال تعریف می شود که قطعا الزامات بیشتری از نظر استانداردهای صنایع غذایی و دارویی از جمله موارد میکروبیولوژیک حائز اهمیت است.
یکی از سطوح استاندارد تدوین شده در تاسیسات دارویی و غذایی با H1 یا گواهی ISO 21469 است که در این سطح از استاندارد تماس اتفاقی روانکار با مواد غذایی وجود دارد.
استفاده از روانکار مناسب در صنایع دارویی با ماشین آلات مدرن به ویژه در خطوط تولید و بسته بندی دارو، آگاهی از محدودیت های بیشتر و الزامات تدوین شده آن ضروری است. در این موارد باید مشخص شود که آیا ماشین آلات باید با روانکارهای معمولی روغن کاری شوند یا اینکه برای انتخاب روانکار مناسب شرایط خاصی وجود دارد.
اداره داروی فدرال ایالات متحده (FDA) مقررات و توصیه های عملی خوب را در مورد تجهیزات تولید دارو و روان کننده ها در چارچوب کد مقررات فدرال (CFR) ارائه داده است. به عنوان مثال در ۲۱ CFR 211.65 تدوین شده است که: «تجهیزات باید طوری ساخته شوند تا سطوحی که با مواد اولیه داروسازی در تماس هستند واکنش پذیر نبوده و افزودنی یا جذب کننده نباشد تا سلامت، ماهیت، کیفیت و خواص محصول از آن متاثر نگردد.
این استاندارد همچنین تاکید دارد که: «هرگونه مواد مورد نیاز برای عملیات، مانند روانکننده ها یا خنککننده ها، نباید با اجزا، ظروف فرآورده های دارویی، دربها، مواد در حال فرآیند یا محصولات دارویی در تماس باشند.»
لذا از این قوانین درمی یابیم که استفاده از روانکار در تاسیسات و تجهیزات تولید دارو اجتناب ناپذیر بوده و البته بایستی به گونه ای مهندسی شود تا با مواد اولیه و محصول تولید شده تماس نداشته باشد و بایستی مسیرهای ایزوله شده دستگاهها روانکاری شوند.
هرگونه انحراف از این دستورالعمل بایستی ارزیابی شده تا اطمینان حاصل شود که هیچ اثر مضری بر تناسب مواد برای استفاده وجود ندارد. تا جایی که امکان دارد، باید از روان کننده ها و روغن های مخصوص مواد غذایی استفاده شود.»
لذا FDA استفاده از روان کننده ها را در یک کارخانه تولیدی یا در بخشهای ماشین جدا شده در صورتی که خطر تماس با محصول دارویی یا بسته بندی آن وجود ندارد، را بلامانع و مجاز می داند.
اگر به هر دلیلی استفاده از روانکار در قسمتی که در معرض فرآورده های دارویی قرار دارد، مورد نیاز باشد بایستی تجزیه و تحلیل لازم انجام شده و اطمینال حاصل شود که برای فرآورده دارویی مضر نبوده و البته حداکثر تماس را تا ۱۰ ppm یا ده قسمت در یک میلیون قسمت تعیین کرده اند.
به طور کلی، اجزای مادام العمر یا غیر روغن کاری شده باید اولین انتخاب برای اجزای ماشین آلات باشند. روان کننده های فود گرید گزینه خوبی برای اجزای ماشین تولید ایزوله هستند که نیاز به روغن کاری دارند. البته، پس از استفاده از روان کننده ها در منطقه تولید، اقدامات تمیزکاری و ضدعفونی مناسب مورد نیاز خواهد بود.
الزامات مربوط به روغن کاری
استاندارد CFR 21.211، FDAتوضیحاتی را در مورد شیوه های روانکاری و نگهداری ماشین آلات مورد استفاده در صنایع دارویی ارائه می دهد که بر اهمیت حفظ تجهیزات تمیز و ایجاد رویه های مکتوب از جمله رویه های روغن کاری تاکید می کند.
اگر تغییر نوعی از روانکار به علت مشکل در کیفیت فرایند صورت گرفته باشد، بایستی کلیه سوابق کتبی مربوط به دسته محصول آسیب دیده نگهداری شود. البته سوابق تعمیر و نگهداری معمولی مانند روغن کاری ایزوله شده الزامی در این استانداردها ندارد.
انتخاب روان کننده
برای انتخاب موثر روان کننده در تاسیسات دارویی، یکی از اولین گامها باید طبقه بندی ماشین آلات بر اساس کاربرد باشد. برای تجهیزات خدمات پشتیبانی که در منطقه تولید قرار ندارند و هیچ تماس بالقوه ای با ماشین آلات تولید یا محصول بسته بندی ندارند، می توان از روان کننده های H2 استفاده کرد که برای کاربردهای غذایی (تماس اتفاقی) در نظر گرفته نشده اند.
این نوع ماشین ها شامل پمپ ها، کمپرسورها، گیربکس ها و سیستم های هیدرولیک درگیر در تامین آب، گازهای فشرده و انرژی می شود. اکثر روان کننده ها (غیر H1) در بازار الزامات H2 را برآورده می کنند، در حالیکه فقط تعداد محدودی دارای ثبت رسمی H2 هستند. اگر یک خط هوای فشرده برای ماشین های تولیدی نیاز به روانکاری داشته باشد، روان کننده H1 انتخاب خوبی خواهد بود.
برای اجزایی مانند راههای کشویی، زنجیر یا نوار نقاله که پتانسیل تماس با محصولات دارویی یا بسته بندی را دارند، تجزیه و تحلیل بیشتر برای شناسایی نیازهای روانکاری واقعی اجزا توصیه می شود. باید تعیین کنیم که آیا این قطعات باید روغن کاری شوند یا خیر، و اگر چنین است، چه نوع روانکار، روش کاربرد و فرکانس مناسب است. به عنوان مثال، یک زنجیر را می توان با روغن، گریس یا اسپری خشک، روغنکاری کرد.
برای روانکاری در اتاقهای ایزوله ممکن است نیاز به استریل کردن ابزارها و اجزای ماشین داشته باشیم. در صورت نیاز به روانکاری، ممکن است نه تنها از روان کننده هایی که قبلاً از طریق عملیات حرارتی (اتوکلاو) یا تابش گاما استریل شدهاند، استفاده شود، بلکه در این موارد، انتخاب روانکار باید شامل الزامات عملکردی اضافی مانند مقاومت در برابر اکسیداسیون، شیمیایی یا تشعشع باشد. همچنین ممکن است به روشهای نگهداری و جابجایی خاصی نیاز باشد.
در صورت امکان، برای حذف روانکاری و همچنین تماس بالقوه روانکار، باید به سمت استفاده از اجزای مادام العمر یا غیر روغن کاری شده برویم. به طور معمول، صنعت داروسازی از ماشین آلات و قطعات نسبتاً کوچکتری نسبت به سایر بخشها استفاده می کند.
در شرایط خاص، یک روان کننده دارای گواهی ISO 21469 ممکن است بر روان کنندهای که به عنوان درجه غذایی H1 ثبت شده است ترجیح داده شود. در حالیکه هر دو طبقه بندی شامل روان کننده های درجه مواد غذایی برای تماس اتفاقی با محصولات است، گواهی ISO “سطح کنترل کیفیت اعمال شده در فرمولاسیون، ساخت، توزیع و ذخیره سازی روان کننده را بررسی می کند تا اطمینان حاصل شود که با بالاترین استانداردهای بهداشتی مطابقت دارد.” هر دو طبقه بندی توسط NSF International مدیریت می شود.
در پایان، حتما از پروتکل های تعیین شده برای مدیریت تغییر پیروی کنیم و تمام شرایط روان کننده، تجزیه و تحلیل آن، تصمیمات و اقدامات انجام شده را ثبت کنیم.
به اشتراک بگذارید:
لینک خبر: